Sulphur / Sulfur Solidification, Forming and handling facilities (Pastillation)
Sulphur / Sulfur Pastillation is another common method for Sulphur / Sulfur Forming & Solidification that has drawn more attention in recent years due to its low impact on the environment. Through Sulphur / Sulfur Pastillation, drops of liquid sulphur are placed on a steel belt cooler in regular rows using a liquid Sulphur / Sulfur Pastillator injector machine. The liquid sulphur loses heat as it moves on the steel belt cooler and forms into uniform hemispherical shapes called pastille.
Since water and sulphur do not come into direct contact with one another through Sulphur / Sulfur Pastillation method, pastillation entails fewer environmental difficulties than other sulphur solidification methods.Sulfur / Sulphur Pastillation is an increasingly popular choice due to its relative ease of setup and high quality end product. Another advantage of Sulfur / Sulphur Pastillator unit is its versatility; the same equipment can be used to create other products, such as Sulphur Bentonite and Urea. Some Sulphur / Sulfur Forming & Solidification plants that use ARIaNA SANAT ZAFARAN CO. pastillators can produce elemental sulphur, Sulphur Bentonite, or other chemical substances pastilles according to prevailing market demand. This versatility also accounts for increasing interest in Sulfur / Sulphur Pastillation unit in production plants around the world.
ARIaNA SANAT ZAFARAN CO. Sulfur / Sulphur pastillators have an operating capacity of 120 tonnes per day, and their modular design allows them to be integrated together to achieve higher production capacity on demand. This modularity Sulfur / Sulphur Pastillator also allows a plant to continue production when one of the units is not operational, while also enabling rapid Sulfur / Sulphur Pastillation unit start-up with lower capital investment costs.
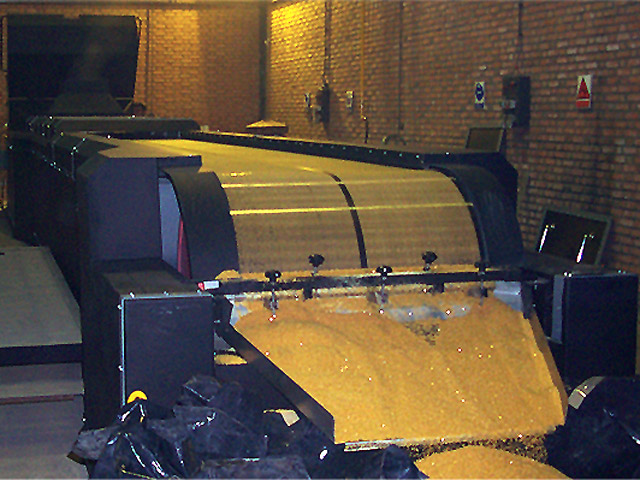
Regardless the name of the unit which are sulfur / sulphur handling, solidifcation or forming unit, after degasification liquid sulphur is stored in a special tank before it is pumped through a 300-micron filter into a Sulfur / Sulphur Pastillation unit. A Sulfur / Sulphur pastillators consist of three main sections: a feeding bar and a stator (both non-moving parts), and a rotor which revolves around them. Liquid sulphur enters the feeding bar and is injected onto a moving steel belt cooler through the holes on a perforated rotor.
Synchronizing of the steel belt cooler speed with the rotor is one of the most important factors affecting the shape of the pastilles and needs to be set precisely at production time of Sulfur / Sulphur Pastillation unit if to ensure a uniform product shape. When properly synchronized, the injected sulphur pastilles form hemispherical shapes as they cool and solidify while moving along the steel belt cooler. The temperature of the steel belt cooler is maintained by controlling the temperature and flow rate of water that is sprayed onto the underside of the belt. This water absorbs the heat from the molten sulphur and then goes to a cooling tower before it is stored in a water tank for re-use at the belt cooler. Based on the climate and temperature of the production plant location, a chiller may be required to supplement the cooling tower. Water never comes into contact with sulphur through this method.
A release agent is applied evenly as a thin layer to the surface of the steel belt cooler to prevent molten sulphur adhesion, to help removal of the pastilles from the surface, and to ensure a uniform pastille shape. The sulphur pastilles have an approximate temperature of 60℃ as they approaches the end of the steel belt cooler, where they are scraped from the belt by a blade and transported by a conveyor to a storage unit. An exhaust air system installed above the cooling belt prevents the spread of sulphur gases away from the pastillator unit.
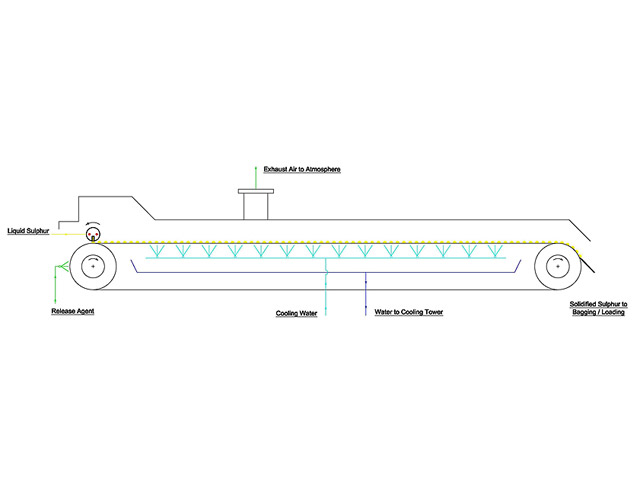
Shape | Pastille ( Hemispherical granule) |
Size | 4 mm diameter - 2 mm height |
Color | Bright yellow |
Angle of repose | 29° |
Dust | Less than 0.4% (wt) |
Bulk density |
Loose: Greater than 1,040 kg/m³ Agitated: Greater than 1,200 kg/m³ |
Standards | Meets SUDIC specifications |
Friability | Less than 2% (Stress Level II) |
Purity | High purity (as received) |
Moisture | Less than 0.1% (wt) |
Others |
Low dust or flake generation during transport Easy to re-melt Stable chemical and physical forms Low acidity Uniform size and shape |
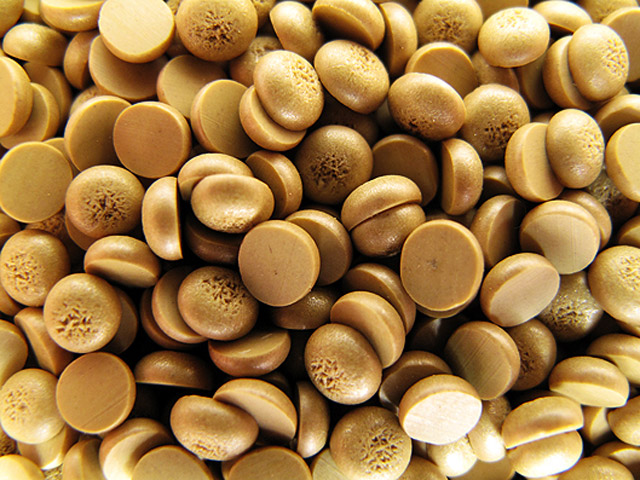
Sulphur Bentonite
Capacity | 5 metric tonnes per hour |
Dimension (mm) |
H: 1,700 W: 2,000 L: 13,000 |
Weight | 5,500 kg |
Utility Consumption |
Electric Power: 20kW Steam: 50 kg/h (3 barg) Water: No net water consumption |
Other Features
- Easy to start up, shut down and operate
- Low maintenance
- Minimal spare part requirements
- Cooling water does not come in contact with sulphur
- No air or water pollution associated with pastille production
- Method enables water circulation
- Minimal plant footprint
- Allows rapid scaling of plant capacity by integration with additional units
- Pastillator versatility also enables the production of elemental solid sulphur, sulphur bentonite and sulphur urea pastilles
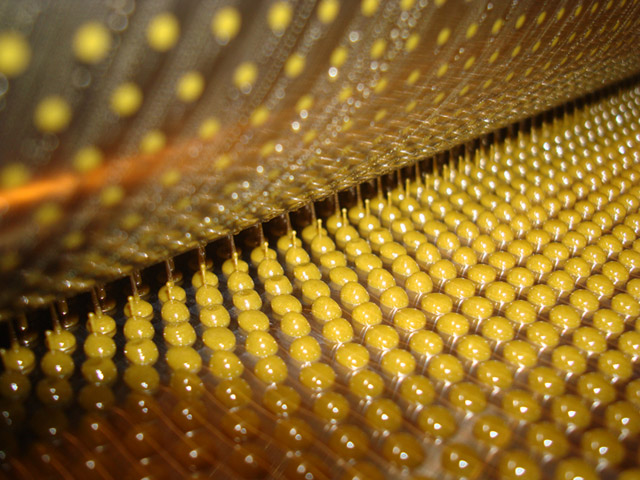